LD25 SILVER/SILVER CHLORIDE EMBEDDABLE REFERENCE ELECTRODE
Note: you can also download a pdf file of the data sheet for the LD25. Click here.
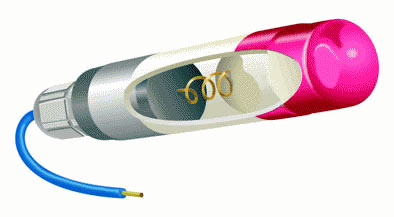
General Description
The LD25 is a long life silver/silver chloride reference electrode with a stable reference potential specifically for permanent installation in reinforced concrete structures. The essential components are silver metal, silver chloride, soluble silver ions and chloride ions.
A sparingly soluble salt, silver chloride, is in equilibrium with a saturated solution of this salt which precipitates in the course of electrolysis. The reversible electrode reaction consists of silver ions going into solution and then combining with the chloride ions to form silver chloride. Thus its potential is determined by the following reactions:
Ag <> Ag + e-
Ag+ + Cl- <> AgCl(s)
Ag + Cl- <> AgCl(s) + e-
The potential is dependent on temperature and the concentration of chloride ions in accordance with the following equation:
Where E0, R, F and T are the standard potential, gas constant, Faraday Constant and temperature respectively. The reaction has been proved to obey these equations in solutions with pH’s of between 0 and 13.5. The potential is however very sensitive to traces of bromide ions which make it more negative.
The electrode element has been prepared by electrolytic precipitation of silver chloride onto silver metal. This has then been embedded in a mortar containing a known concentration of chloride ions and an anti-drying agent. The housing consists of a white nylon barrel, white nylon inserts, and a cable gland rated at IP68.
Specification
Element Type:
Ag, AgCI(s), CI-, Ag+
Typical 3g silver per electrode
Potential:
-15Mv +/-10Mv versus the Saturated Calomel Electrode (SCE)
230Mv +/-10mV versus the Standard Hydrogen Electrode (SHE)
Drift:
less 3mV in 24 hours.
Typically less than +/-10mV expected in 20 years
Note: The potential drift is subject to temperature, Donnan potential and liquid junction potential changes within the surrounding environment which may mask any changes produced by the electrode itself.
Internal Resistance:
Less than 2kOhms
Polarisation Characteristics (determined galvanostatically in sodium hydroxide solution)
2mV potential shift after the application of 0.1μA for 30 seconds.
12mV potential shift after the application of 1μA for 30 seconds.
Dimensions:
75 mm long x 24mm diameter
Cable gland 20mm long x 15mm diameter.
Housing:
White Nylon Barrel
White Nylon Inserts
Cable Gland IP68
Cable:
Supplied to order
Expected life:
More than 57 years at a leakage current of 1mA will result in the loss of 2 grams of silver. The functional life of the electrode will most likely to be determined by the life of the associated cables.
Other Features:
Large Measuring Interface (>450mm2)
Anti Drying agent
Installation Procedure
The purpose of this statement is to ensure that the reference electrodes when delivered to site are correctly stored, checked for functionality and installed.
Storage
The electrodes are individually numbered and delivered to site boxed with the red protective caps in place. The purpose of the caps is to protect the sensor end of the electrode from contamination or damage whilst in storage. With the delivery inside the box there will be a calibration certificate for all the delivered electrodes. This document should be kept with the record documents for the contract. The calibration certificate is a record of the individual reference potentials measured against a saturated calomel electrode (SCE) at 20oC under laboratory conditions. The Corrosion Engineer may refer to the information on the calibration certificate during the operation of the monitoring system.
The electrodes should be checked to ensure that they match the order and stored with the red caps in place in a safe, dry place within a temperature range of 0oC and 45oC. It is important to ensure that the electrode and its cable are protected from physical damage.
Pre installation Functional Check
The purpose of this procedure is to check that the electrode potential is stable.
Prepare a solution of 3% salt solution; 30g of sodium chloride (salt) per 1 Lt of water. Remove the cap from the electrode and soak the tip of the electrode in the solution for a minimum of 2 hours and maximum of 3 hours.
After soaking the electrode measure the potential using a calomel electrode (SCE) with a digital voltmeter at 10mohm and 1000mohm input impedance with the SCE connected to the positive/common terminal and record the results. The potentials should be steady and in the range +/- 20mv of the calibrated values.
A satisfactory alternative to using a saturated calomel electrode would be to check the soaking electrode potentials against each other or use one extra electrode as a test electrode.
Once the electrode is checked it should be removed from the solution, the cap carefully replaced and it should be installed within 48 hours.
Electrode Installation
Procedure :-
- Breakout the concrete at the electrode position to expose the reinforcement and blow out all the debris
- Tie the electrode alongside the reinforcement using a plastic cable tie and temporarily support the cable
- Make a record of the electrode number and remove the red cap
- Thoroughly wet the concrete and remove the surface water
- Make good the concrete using a suitable conductive cementitious repair mortar being careful to ensure that the electrode is fully encapsulated (do not use any primers for the reinforcement or concrete )
- After the mortar has cured check the electrode stability using a digital voltmeter at 10mohm and 1000mohm input impedance. Connect the common lead (black) to the electrode and the red lead to the steel. The reading should be steady and not drift or fluctuate during a 5 second measuring period. If the potential drift towards zero on the low input impedance it implies that the electrode contact is poor. If it drifts on the high input impedance setting it is advisable to check that there is no damage to the cable.
The important points to remember are that the concrete should be pre-wetted , the red cap removed and the cable supported while the concrete is placed and cured. The electrode-measuring tip must be fully encapsulated by the repair mortar.
Variations on this procedure can be acceptable subject to agreement by the Design engineer. In some cases the concrete is cored and the electrode placed in the core hole with the concrete then made good. At other times to ensure good contact the electrodes are pre-potted in a mortar cylinder before embedding in the concrete.
Copyright © 2006 [Castle Electrodes]. All rights reserved.

|